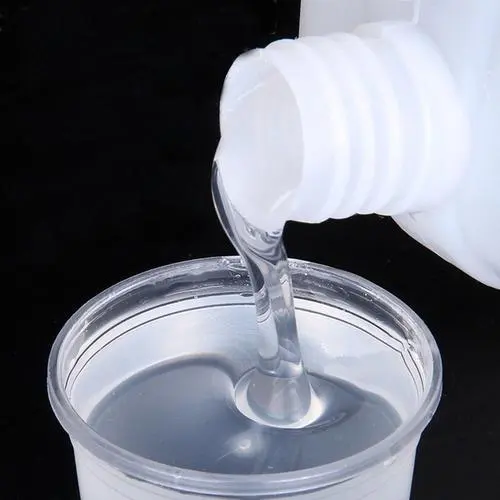
In the complex world of industrial chemicals, Hydroxypropyl Methylcellulose (HPMC) has emerged as a vital component across multiple sectors. Whether you’re in construction, pharmaceuticals, food, or cosmetics, choosing the right HPMC is crucial for the success of your products. Here are some key factors to consider when making this important decision.
1. Understand Your Application Requirements
Construction Industry
- Mortar and Plaster: If you’re using HPMC in mortar and plaster, you need a product that excels in water – retention and workability. Look for an HPMC grade with a high water – retention capacity. This will ensure that the mortar or plaster remains wet and workable for a longer time during application. A good HPMC for this purpose should also enhance the adhesion of the mixture to the substrate, reducing the chances of cracks and improving the overall strength of the bond.
- Tile Adhesives: For tile adhesives, viscosity and slip resistance are key. The HPMC should thicken the adhesive enough to prevent tiles from slipping during installation, even on vertical or uneven surfaces. Consider an HPMC with a medium to high viscosity range that can provide the necessary tackiness and stability for tile – laying operations.
Pharmaceutical Industry
- Tablet Coating: When using HPMC for tablet coating, you must match the type of coating required. For immediate – release tablets, a fast – dissolving HPMC grade is ideal. Delayed – release and sustained – release tablets need HPMC formulations that can precisely control the drug release rate. Pay attention to the film – forming properties of the HPMC, as a strong and uniform film is essential for protecting the active ingredients and ensuring proper drug delivery.
- Suspensions and Emulsions: In pharmaceutical suspensions and emulsions, HPMC acts as a stabilizer. You need an HPMC that can effectively prevent the separation of components and maintain the uniform distribution of active ingredients over time. Look for grades with good emulsifying and stabilizing capabilities, which are often specified by the manufacturer in terms of their ability to reduce particle sedimentation.
Food Industry
- Bakery Products: In bread and cake making, HPMC is used for moisture retention and dough conditioning. Select an HPMC that can significantly extend the shelf – life of baked goods by keeping them moist. It should also improve the elasticity of the dough, making it easier to handle during the baking process. Consider HPMC products with a proven track record in enhancing the texture and softness of bakery items.
- Dairy Products: For dairy products like yogurt and cheese, HPMC helps in preventing syneresis. Choose an HPMC grade that can effectively control the consistency of the dairy product, maintaining its smooth and creamy texture. It should be compatible with the acidic environment of dairy products without affecting their taste or quality.
Cosmetic Industry
- Skincare Products: In creams, lotions, and serums, HPMC plays a role in texture control and active ingredient delivery. You need an HPMC that can provide a smooth and non – greasy feel to the product. It should also enhance the spreadability of the skincare product on the skin and improve the adhesion of active ingredients. Look for HPMC grades that are specifically formulated for cosmetic applications and are safe for use on the skin.
- Haircare Products: For shampoos and conditioners, HPMC is used for thickening. Select an HPMC that can effectively increase the viscosity of the haircare product without making it too thick or difficult to dispense. It should also contribute to the hair – conditioning effect, leaving the hair feeling soft and manageable.
2. Evaluate Quality Parameters
Viscosity
Viscosity is a critical parameter for HPMC. Different applications require different viscosity ranges. In construction materials, a higher viscosity HPMC may be needed to improve the workability and adhesion. In pharmaceutical suspensions, a lower viscosity HPMC might be suitable to ensure easy pouring and uniform mixing. Always check the viscosity specifications provided by the manufacturer and ensure they align with your application requirements. Viscosity can be measured using standard laboratory methods such as viscometry, and reputable manufacturers will provide accurate viscosity data for their products.
Purity
High – purity HPMC is essential, especially in applications where safety and performance are crucial, such as in pharmaceuticals and food. Impurities in HPMC can affect the quality and functionality of the final product. Look for HPMC products that are produced using advanced purification processes and have a high degree of purity. The manufacturer should be able to provide detailed information about the purity level, including the presence of any residual solvents or contaminants. Third – party certifications, such as those from regulatory bodies like the FDA (in the case of pharmaceutical and food applications), can also be an indication of high – quality, pure HPMC.
Particle Size
The particle size of HPMC can impact its solubility and dispersion in different media. Finer particle sizes generally result in faster dissolution and better dispersion. In applications where quick dissolution is required, such as in some pharmaceutical formulations or food products, choose an HPMC with a smaller average particle size. However, in certain construction applications where a more granular texture might be beneficial for handling, a coarser particle size could be acceptable. Manufacturers usually specify the particle size distribution of their HPMC products, which can help you make an informed decision.
3. Consider the Manufacturer’s Reputation
Experience and Expertise
Choose a manufacturer with extensive experience in producing HPMC. An experienced manufacturer is more likely to have refined their production processes over time, resulting in a higher – quality product. They will also have a better understanding of the different applications of HPMC and can provide valuable technical support. Look for manufacturers who have been in the industry for a significant number of years and have a proven track record of supplying HPMC to various sectors.
Quality Control Measures
A reliable manufacturer will have strict quality control measures in place throughout the production process. This includes regular testing of raw materials, in – process monitoring, and final product testing. The manufacturer should be able to provide documentation of their quality control procedures and test results. ISO 9001 – certified manufacturers, for example, follow international quality management standards, which is a good indication of their commitment to quality.
Customer Reviews and References
Check for customer reviews and references from other companies that have used the manufacturer’s HPMC products. Positive reviews and testimonials can give you confidence in the quality and performance of the product. You can also reach out to other industry professionals or trade associations for recommendations on reliable HPMC manufacturers. A manufacturer with a strong reputation for customer satisfaction is more likely to provide a product that meets your expectations.
4. Pricing and Supply Chain
Cost – Effectiveness
While price should not be the sole determining factor, it is an important consideration. Compare the prices of HPMC from different manufacturers, but also consider the quality and performance of the product. A lower – priced HPMC may seem attractive, but if it does not meet your quality requirements, it could end up costing you more in the long run due to product failures or inefficiencies. Look for a balance between price and quality, and consider the overall cost – effectiveness of the product in relation to your production needs.
Reliable Supply Chain
Ensure that the manufacturer has a reliable supply chain and can meet your production demands consistently. A disrupted supply of HPMC can lead to production delays and financial losses. Consider factors such as the manufacturer’s inventory management, shipping capabilities, and their ability to handle large orders. A manufacturer with a global presence and multiple production facilities may be better equipped to ensure a steady supply of HPMC, even in the face of unforeseen circumstances.
In conclusion, choosing the right HPMC requires a careful evaluation of your application requirements, quality parameters, the manufacturer’s reputation, and pricing and supply chain factors. By taking the time to consider these aspects, you can select an HPMC product that will optimize the performance of your products and contribute to the success of your business.